YP Newsletter Highlight: Wasted Space Written by Abby Lichtscheidl
- SWANA Badger Chapter
- Nov 13, 2019
- 4 min read

Abby Lichtscheidl graduated from UWSP in December of 2017 with a BS in soil and waste resources. While in school, she was an intern at the Marathon County Solid Waste Department and is now a full time Waste Specialist for the county.
At work, she operates heavy machinery for daily operations and does general site maintenance.
When she’s not working, Abby keeps busy by attending group fitness classes at the YMCA, going to local community events, and spending time with her cat, Tilly.
A Look Into Maximizing Efficiencies at Marathon County Solid Waste
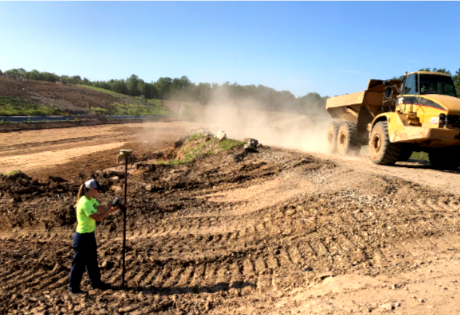
The new age of solid waste is here! We are constantly integrating new technology into the industry in an effort to more efficiently manage our waste. One form of technology is a Global Positioning System (GPS). GPS’s aren’t only used to get you from A to B, the solid waste industry utilizes it daily! It’s mostly associated with landfill construction, but here at Marathon County Solid Waste (MCSW) our main use is for daily landfill operations.
MCSW has two machines on site equipped with GPS: the compactor and bulldozer and a separate rover. Each machine utilizes the GPS in different ways. The compactor uses the GPS for rough elevation and compaction data. The bulldozer is for fine elevation changes, and the rover is used for designing special projects and construction quality assurance (CQA) work.
The majority of the time we use the GPS in the compactor. It gives us a constant data stream of elevation and compaction data in real time. This information is important because when creating new lifts, we need the surface to be solid and uniform. This is not only an efficiency aspect, but a safety one as well; an uneven surface can result in poor driving areas and vehicle rollovers. There’s a function in the GPS system called flatpad that we often use when creating new lifts. You simply enter in the desired elevation and the GPS creates a “flat pad” for the entire area of the landfill. From then on the screen shows you the cut/fill of the point where the machine is sitting. The accuracy on our cut/fill data is within a tenth of a foot!
While compacting, the screen also shows a color coded grid indicating the density of the surface. It compares how much deflection there is to the previous time that same area was rolled over. In addition to the compaction grid, a daily compaction report is created and then emailed to all operators. Entering the daily tonnage of garbage calculates the waste density of the working area for each specific day.
This allows us to try new techniques and fine tune our compaction methods to fully maximize the airspace we are filling. Moisture, temperature, waste type, machine speed, lift height, and skill all play a role in the science (and art) of waste compaction. All that being said, our current compaction rates are around 1,800 pounds per cubic yard.
Last year, MCSW experienced trouble with rainwater collecting in low areas of the landfill. Uneven settlement and different waste types resulted in multiple low areas and uneven surfaces. Contrary to what many might think, a landfill doesn’t close when it rains 3” during the spring thaw, and we do not have blacktop access to our active working face. These low areas caused significant operational issues with traffic flow and stuck vehicles. To combat, we used the GPS to create a slope file instead of using a flatpad

for our new lift. We wanted rainwater to shed rather than collect and saturate the traffic areas while still staying in the landfill. This is when we utilize the rover to design our grades. We marked the elevations on a previous cell and used the elevation of the current lift to determine what percent slope would work the best. A 1% slope seems like a small percentage, but when cast along 500 feet horizontally, it means a drop of 5 feet vertically across the surface. Once we determine the percent slope desired, we save the file and it can then be downloaded to every machine on site. With the new sloped surface directing stormwater away from traffic areas, we’ve seen less accumulation of rainwater on the landfill surface, decreased drying time after rain events, and greater efficiency in traffic flow throughout the working area.
The GPS works off a solar powered repeater system comprised of nodes. Each machine has a node, along with four nodes strategically placed throughout the site. For the machines to retrieve the instantaneous data they must be connected to the base station. Everything communicates via line of sight. As you can see in the picture, there is not a direct line of sight from the machines to the base, thus the stationary nodes must pick up the machines signal and repeat it back to the base.
We find significant value in the GPS every day. We can monitor density on a daily basis and find trends that may influence compaction. When creating new lifts or outside banks, we don’t have to rely on eyeballing; we have a sure way of telling if the surface is up to grade. Looking at the life cycle of building a landfill, GPS has always been utilized in the initial liner construction and capping process, however, we now utilize it while filling to make daily operations more efficient. With strict DNR regulations, focus on maximizing airspace, and increased cost for constructing a new landfill, it is in our best interest to utilize the technology available in an effort to better manage the challenges of landfill operations, while protecting human health and the environment.

Diagram shows how the machines in the landfill are able to communicate with the base.
Comments